THE ENERCLEAR METHOD:
How it Works
WHEN IT COMES TO PIPELINE PROTECTION & RESTORATION, WE KNOW WHAT TO DO
Our three-step method cleans, prepares, and coats your pipeline with meticulous attention to detail to ensure an even, durable finish and enhancement to the lifespan of your lines.
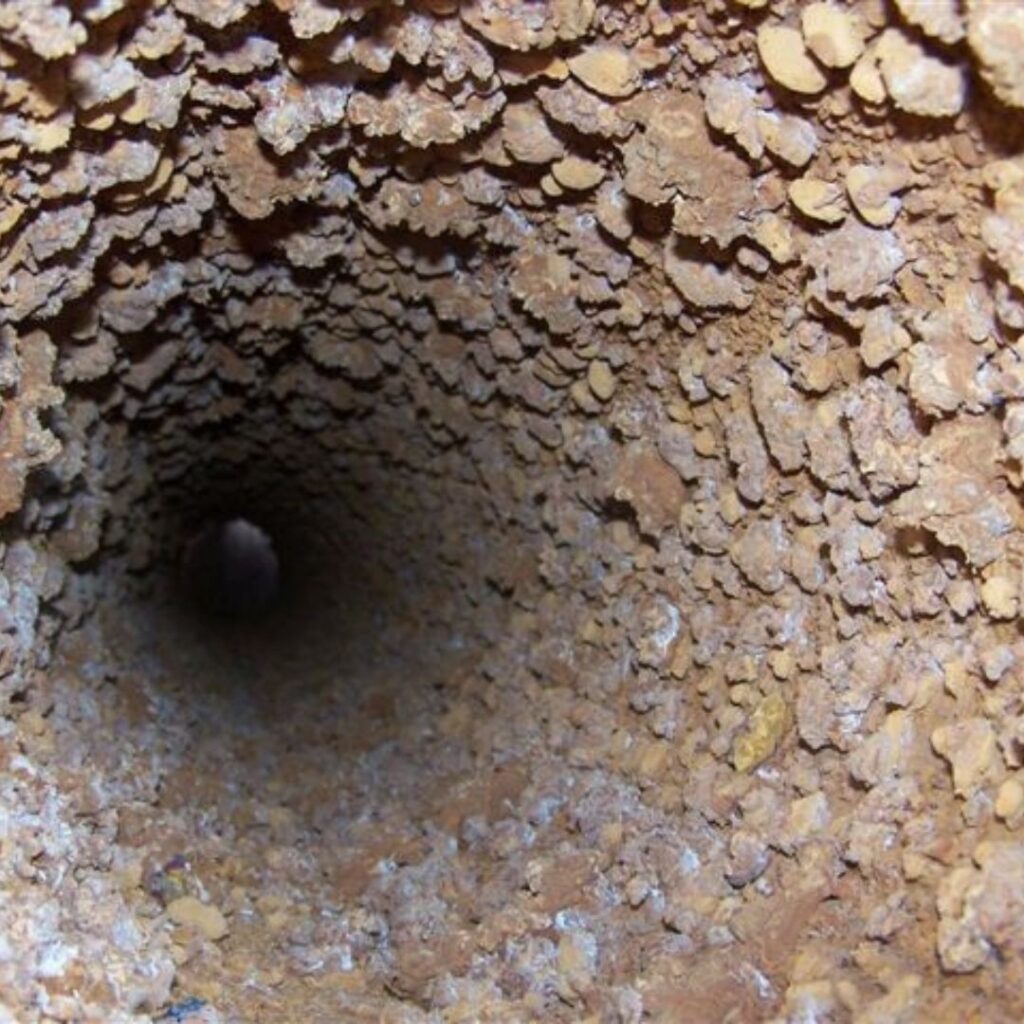
1
Cleaning
1
Cleaning
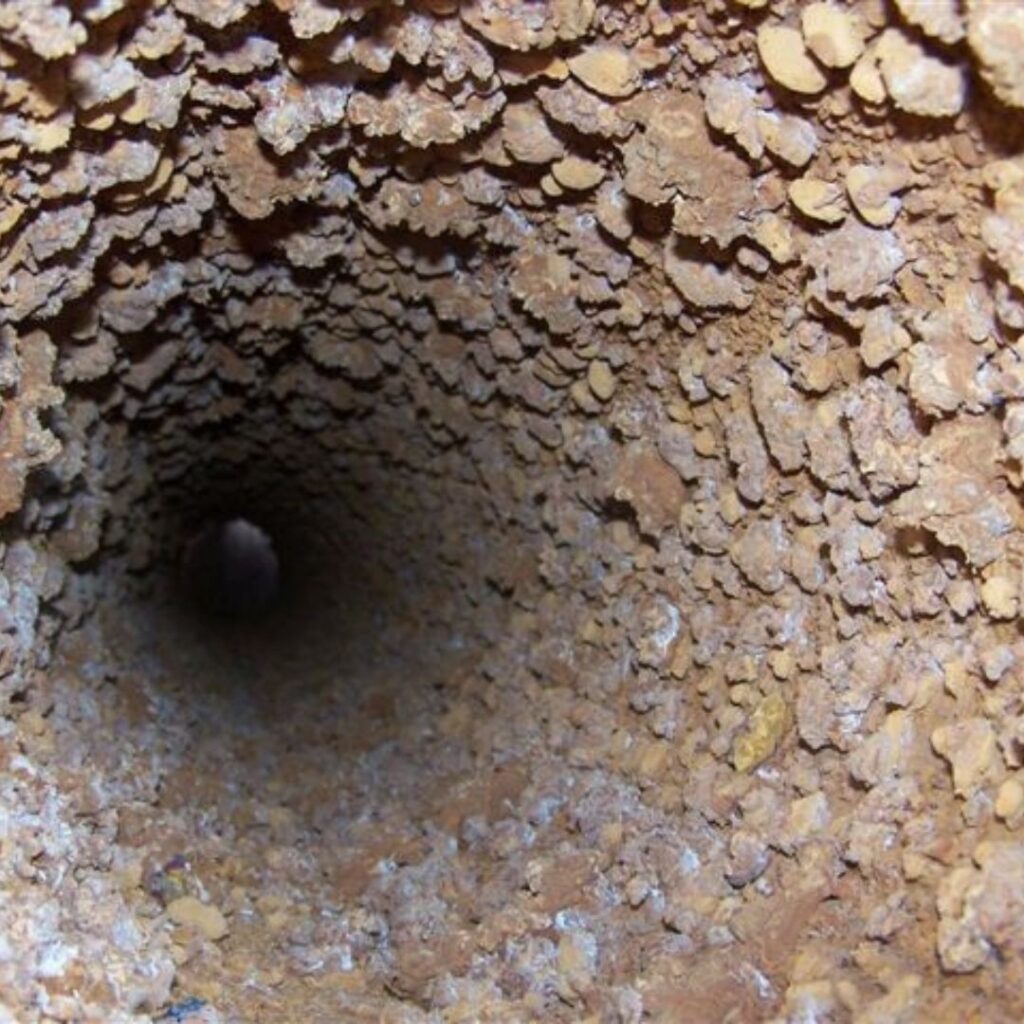
STEP 1: MECHANICAL CLEANING
Mechanical cleaning program methodology is designed based on specific pipeline conditions with the intent to “peel the onion” and get the substrate to bare metal.
- Mechanical pigs propelled by dried compressed air move throughout the line
- This process uses various pigs carrying soap/water to "flush and brush"
- Various solvent blends utilized to enhance the mechanical cleaning process
- Repeat cleaning procedure as necessary
MECHANICAL CLEANING
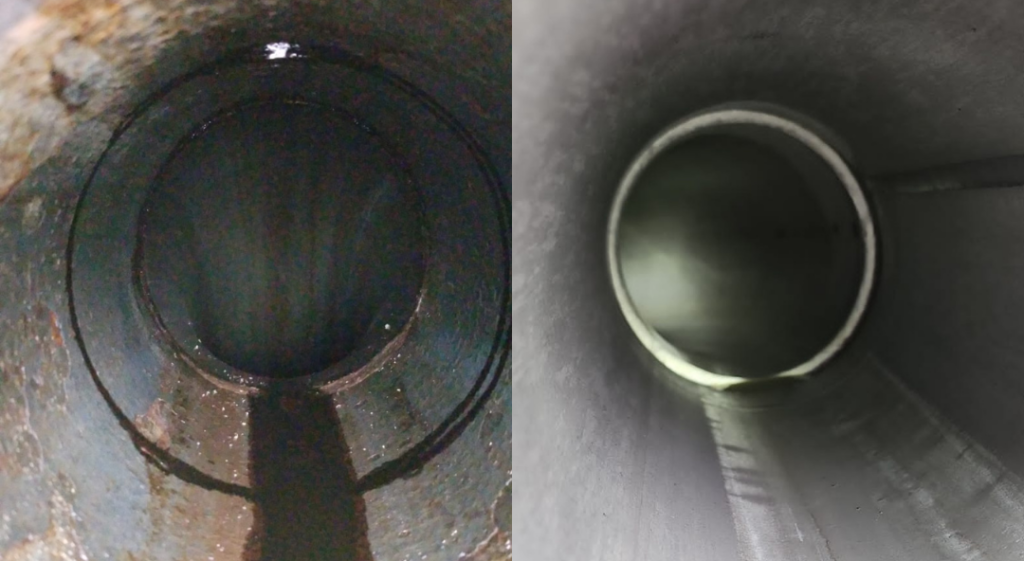
Our robust mechanical pigs scrub away tough debris, rust, and scale, ensuring a thorough physical clean.
Following up with our specialized chemical treatments, we dissolve and flush out any remaining contaminants, ensuring no residues are left behind. We use a progressive pigging process to ensure lines run as clean as possible.
This dual-action process not only minimizes downtown but prepares your lines for the chemical preparation phase.
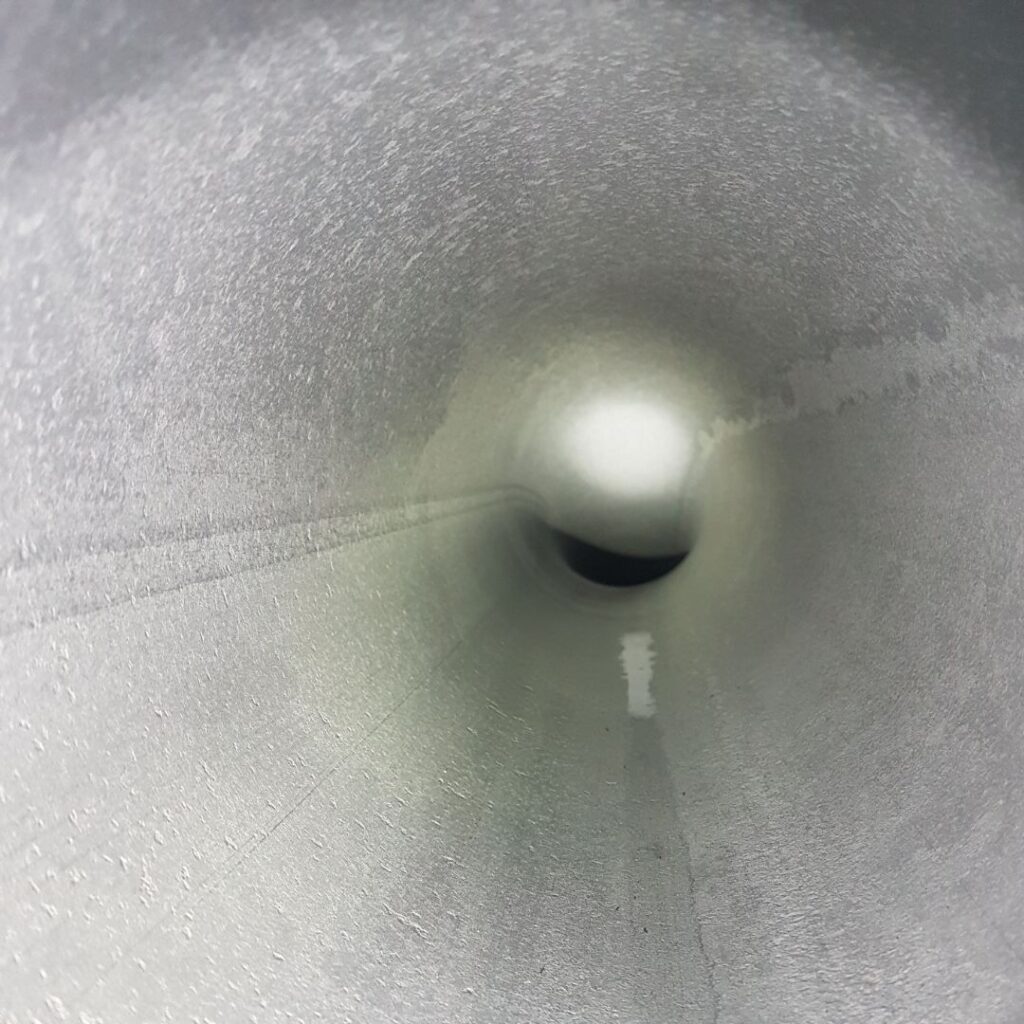
2
PREPARATION
2
PREPARATION
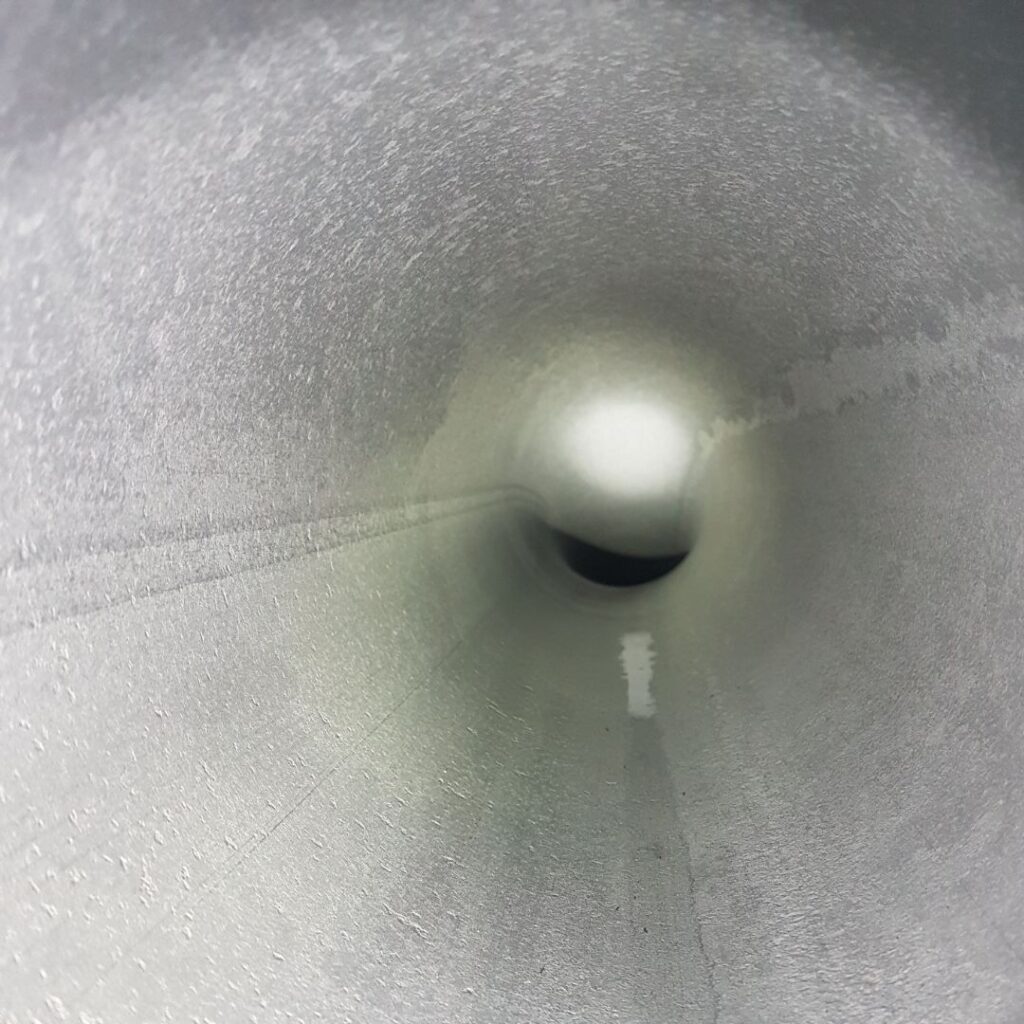
STEP 2: CHEMICAL PREPARATION
This step of our process ensures the internal surface of your lines is prepared for the final coating stage. We use a chemical cleaning technique to clean and acid etch the lines to achieve a near-white metal finish and complete a rigorous quality control protocol.
- Batch inhibited HCI between two pigs under pressure
- If required, we will complete additional mechanical and chemical cleaning
- The result is a line that has achieve NACE #1 or NACE #2 visual finish
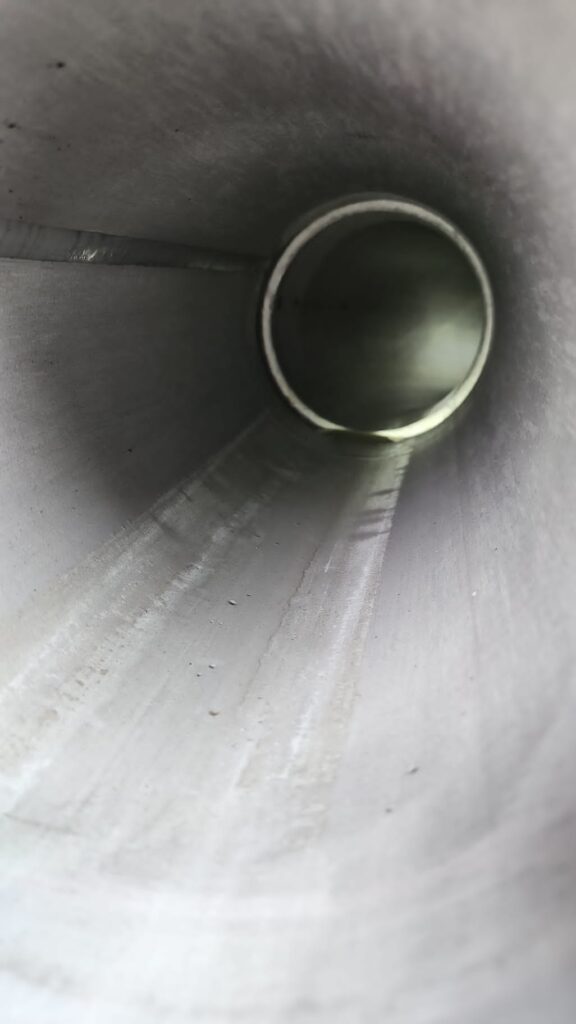
After the surface preparation is complete, the pipe is cleaned free of any debris, chemically balanced, and dried in preparation of the coating application. All of our work is documented to ensure we follow the applicators procedure criteria for preparation.
This dual-action strategy not only minimizes downtown but prepares your lines for our epoxy coating which significantly enhances performance and lifespan.
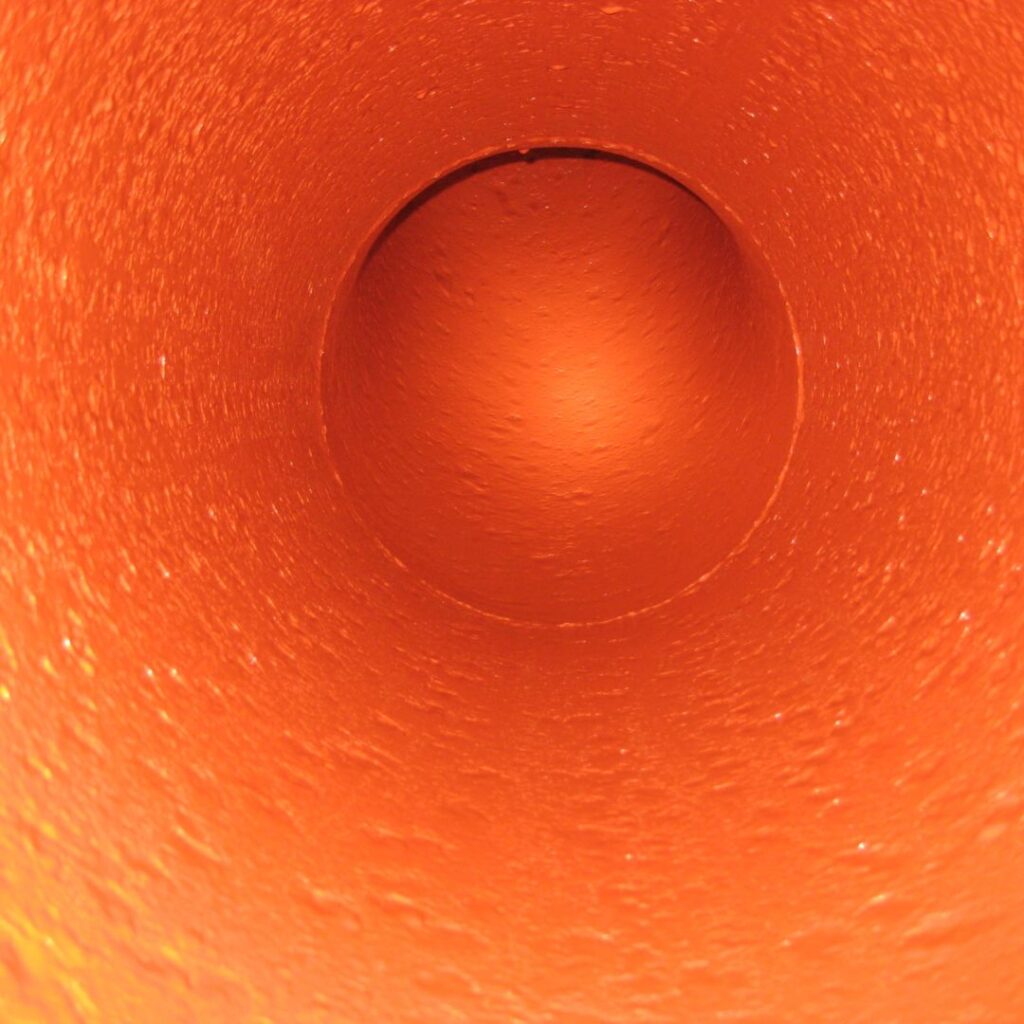
3
Coating
3
Coating
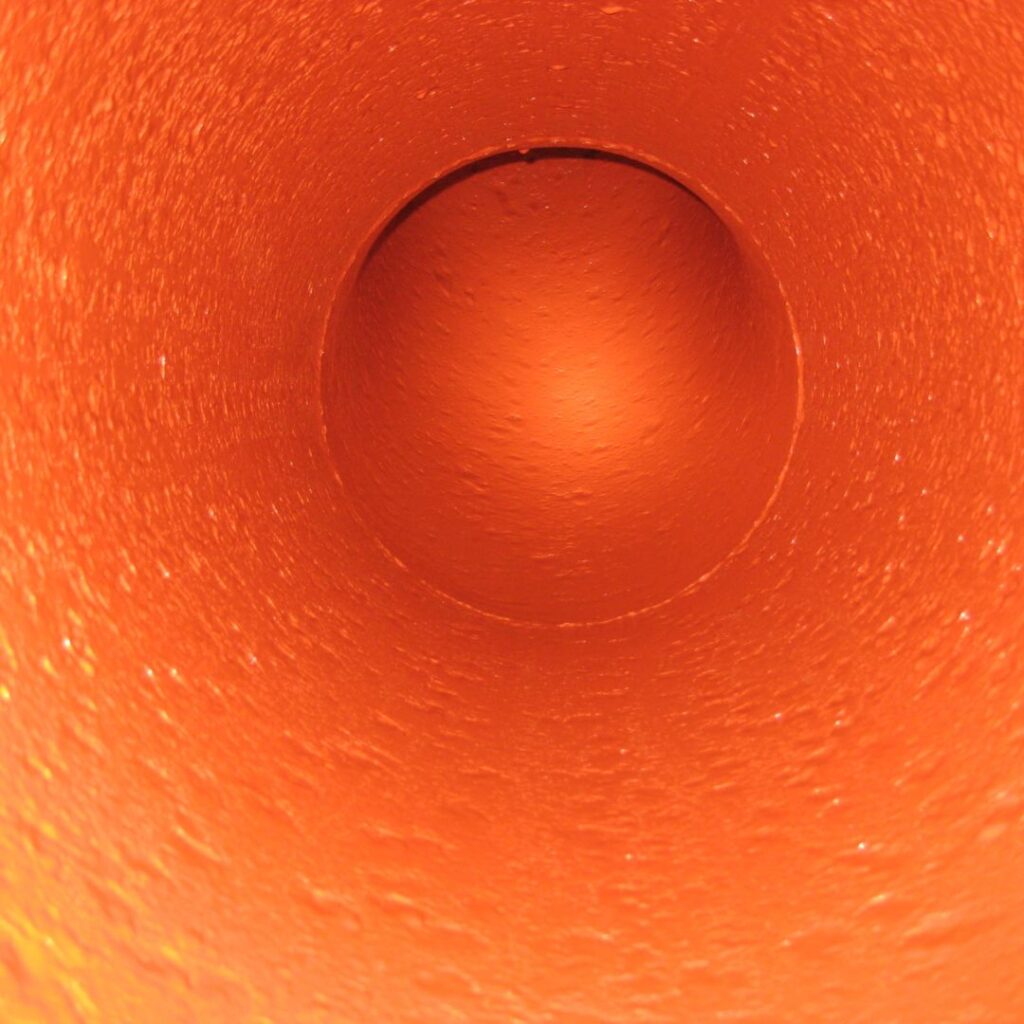
STEP 3: COATING
Our Multiple Pass Flood Coat System is a new iteration of a proven technology developed in the ‘70s. Using specially designed pigs propelled with dried compressed air, the pipeline is uniformly coated and then cured before being returned to service.
- Prepare the coating as specified by the manufacturer
- Load coating required between two coating pigs
- Using back pressure, the batch is sent down the line
- Re-coat (depending on the line length/size) within 12-24 hours
EVEN COATING

Our two-part epoxy coating is mixed and loaded between two pigs. As it moves down the line, a slug/pill places pressure on both ends at a controlled rate of travel, by utilizing our Multiple Pass Flood Coat System. This allows for uniform coating coverage on the line, even where pitting is present. After every pass, we undertake a detailed quality control procedure to measure the dry film thickness and ensure the coating is properly applied.
CURING
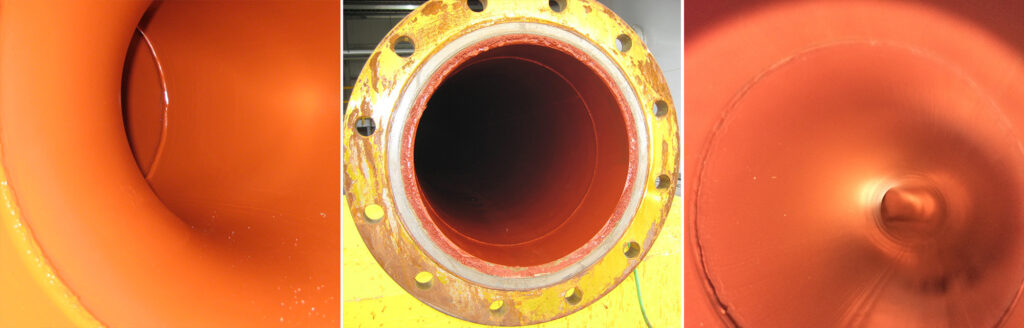
We force cure the line by blowing warm air down the pipeline.
The result? Pipelines that are cleaned, coated, and are integrally sound for decades to come.